
Today, tuners and designers rely on computer software which computes a port’s specific time area (STA). General insights into a cylinder’s performance can be made by characterizing attributes such as the timing of the exhaust and transfer ports, the port widths, and the directional flow angles, but a deeper analysis is required to truly optimize a cylinder. Typically, dirt bike engines commonly feature bridge port or triple port designs. Similar to the transfer ports, the duct shape, angle, length and volume have a large influence on how well gases can flow through the port. The exhaust ports dictate how much and how well exhaust gases depart the cylinder. The transfer ports also help cool the piston. The shapes and flow capabilities of the transfer ports play a big part in how effectively the cylinder can be scavenged of exhaust gases and filled with fresh air and fuel. To a lesser extent, the downward motion of the piston also aids in creating a pressure differential between the crankcase and cylinder. As the transfer ports begin to open, the exhaust pipe sucks fresh mixture up through the transfer ports into the cylinder. Once the piston uncovers the tops of the transfer ports the blowdown phase is complete, at which point much of the exhaust gas has been expelled from the cylinder.
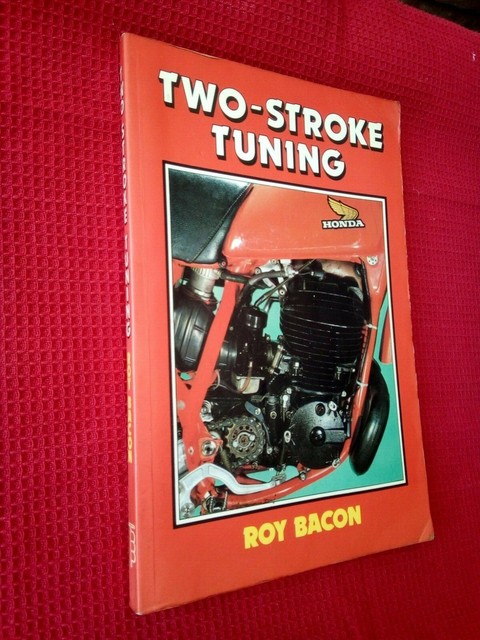
This occurs as the piston travels downward after the cylinder has fired. The transfer ports are responsible for moving fresh air and fuel up from the crankcase into the cylinder.
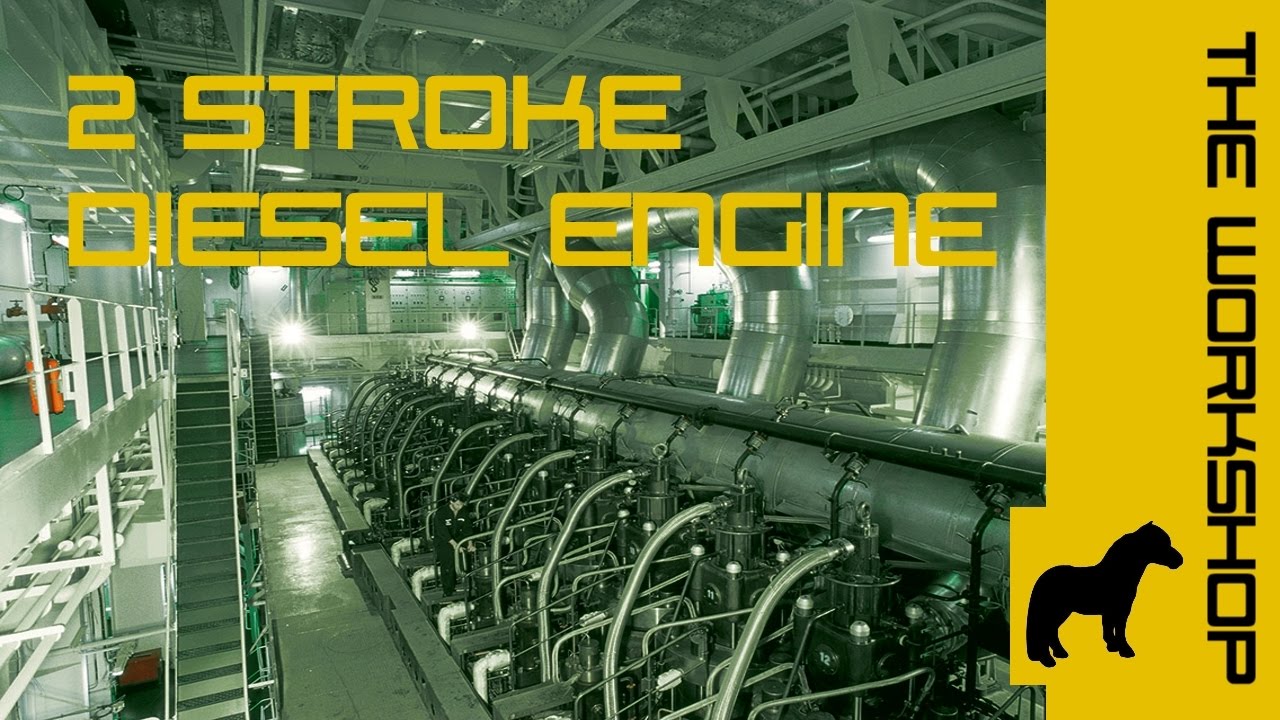
In this case, the primary restriction in the inlet port is the reed valve and as such the valve’s geometry and flow capabilities often dictate the inlet port's performance. On modern machinery, the inlet simply connects the reed valve to the cylinder or crankcase.
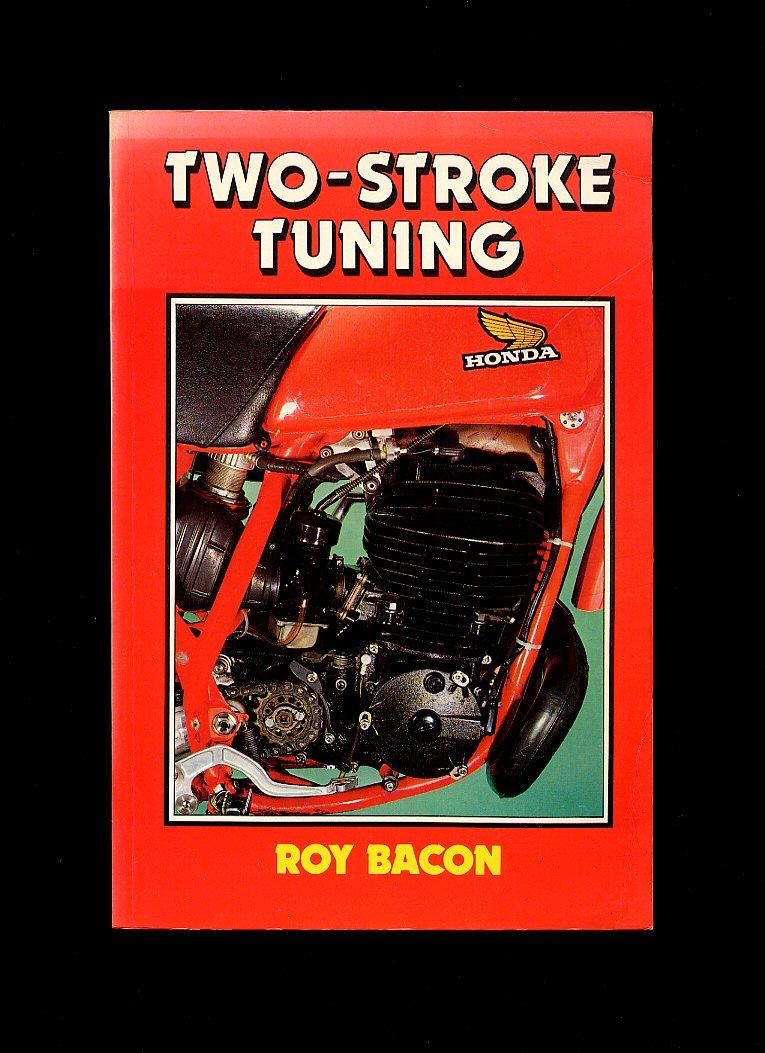
On older engines, a rotary valve or the piston may also be used to control the opening and closing of the inlet port.

The inlet port/passage delivers air into the engine’s crankcase, most commonly through a reed valve, on a dirt bike engine.
